Manufacturing
Patented Technologies, Unsurpassed Quality
TPM has developed proprietary manufacturing processes that include custom-designed mills built specifically for the production of perforated tubing. We continually refine our equipment and procedures to ensure your products perform reliably in the field and deliver maximum value for you.
TPM manufacturing processes use spiral welding, a more demanding, but superior-quality technique. We’ve fine-tuned every aspect of our production process, down to the custom-blended gas that enhances the quality of our weld seams.
Spiral Welding Advantages
The TPM spiral welding process is superior to conventional welding in the following ways:
- Flexibility in handling a wide variety of designs/configurations
- High strength
- Greater rigidity at reduced wall thicknesses
- Ability to produce large-OD tubes
- Unlimited tube lengths
- Production efficiency in short runs
Support Services
TPM can manage all aspects of production and coordinate any additional services you need:
- Design
- Component assembly
- Inventory management
- Shipping logistics
- Packing and crating (including export crating)
- Heat treating
- Electropolishing
- Coatings
Quality
TPM adheres to stringent quality assurance procedures, including 100% inspection of finished pieces. Every tubing joint receives a thorough examination of ID/OD, weld integrity, straightness, and length. TPM is able to validate the micron rating in our finished product.
TPM will also incorporate any additional quality requirements you may have. The TPM quality assurance program is fully documented and available for your review.
Material certifications are provided for every order, with complete listings of relevant chemical and physical properties. Every order is fully traceable back to the heat number of the raw material.
Production Capabilities
TPM production capabilities accommodate a wide range of product designs and sizes. We have multiple modular production lines, each of which can be quickly re-tooled to handle large volumes or special requirements.
Dimensions
- Diameters: .625 in. OD (15.875 mm) to 15 in. OD (381 mm)
- Wall Thicknesses: .025 in. (.635 mm) to .1875 in. (4.763 mm)
- Lengths: Custom lengths, plus stock lengths from 2.5 in. (63.5 mm) to 38 feet (11.582 m)
Materials
- Stainless steel and mild carbon steel
- Titanium, nickel, HASTELLOY® and other exotic alloys
Perforation Patterns
- Custom hole shapes, sizes, and patterns to suit any open-area requirement
- Inventory of standard staggered and in-line patterns
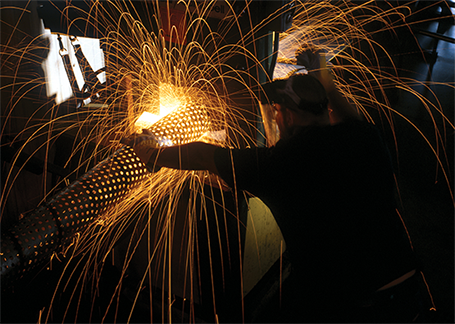
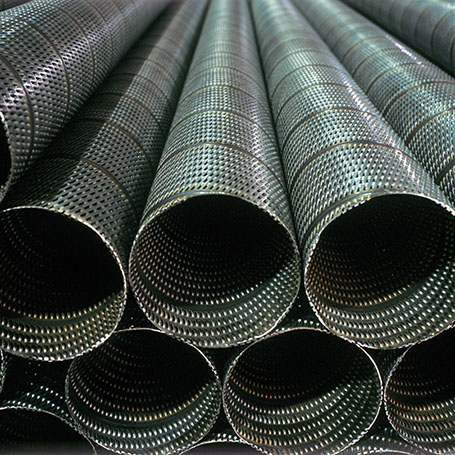